Fastener Study Yields Navy Supply Efficiencies
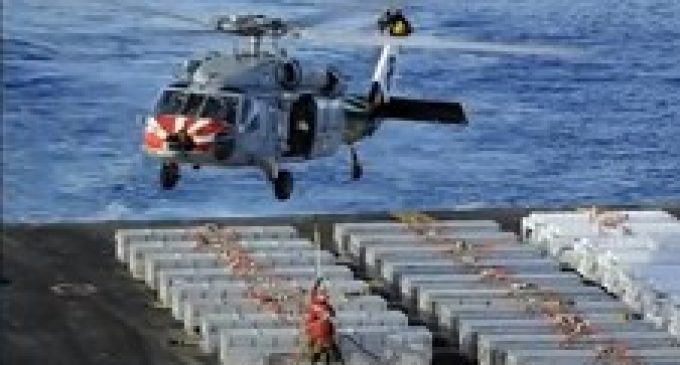
4/23/2013 1:20:00 AM
FEATURE
Joseph Battista
NSWCCD-SSES Public Affairs
MEDIA SPOTLIGHT – Naval Sea Systems Command completed a fleet-wide fastener study, identifying and recommending the removal of thousands of fasteners from the Navy supply system, NAVSEA announced April 18.
The 16-week supply system review identified 108,000 dormant fasteners-fasteners with no contract, requisition or maintenance history in the past five years-and 3,200 duplicate fasteners where two or more identical fasteners had different stock numbers.
The NAVSEA Commonality Project management team led the study, collaborating with in-service engineering agents, technical warrant holders, program offices, shipyards, shipbuilders, the Defense Logistics Agency and original equipment manufacturers.
“This fastener deep dive focused on basically anything used to secure two things together on a ship,” said Bill Moss, Commonality Project Management Team lead with NSWC Carderock’s Ship Systems Engineering Station (SSES) in Philadelphia. “This includes all the nuts, bolts, rivets, and pins.”
John Sofia leads the NAVSEA commonality program established in 2007 to find cross-platform cost savings and avoidance opportunities.
The Defense Logistics Agency documents the cost per year to maintain a stock number is between $200 and $500 each, said Tessa Kashuba, a member of the Commonality Project management team.
“The savings may seem small, but when taken in context to the number of dormant and duplicate [stock numbers], the cost escalates rapidly,” said Kashuba. “However, we have to be careful when we remove an item because we don’t want to eliminate something that’s still needed. For example, we may discover a fastener that hasn’t been ordered in a number of years, but then find out a ship is coming into an availability period that may require that fastener.”
Another focus of the study was to work with shipbuilders and shipyards to familiarize them with NAVSEA’s Virtual Shelf. Virtual Shelf is an electronic repository of standard architectures, design guidelines, specifications and parts lists for ship systems.
“Shipbuilders may go directly to vendors to purchase fasteners during ship construction,” said Dana Melvin, Commonality Project team member. “The fasteners they purchase may not have a [stock number], and must be added into the system if there isn’t a comparable fastener available. Our goal is to get the builders to use fasteners that already have [stock numbers].”
Fredrick Kachele, Metallurgy and Fasteners Branch subject matter expert, said shipyards machine their own fasteners, or do a local small-quantity purchase, when they cannot find a [stock number] for the fastener they need. Both options are very expensive, but NAVSEA’s Virtual Shelf can help users find required, qualified equipment at lowest total ownership cost.
“The Virtual Shelf eliminates hours of fruitless searches for a part,” said Kachele. “It leads the searcher to a comparable fastener that will meet their needs. Prior to this, there was no reliable way to find a replacement part without knowing that NSN. New items purchased outside of the Virtual Shelf may need to go through qualification testing, which costs the Navy money.”
For more information about the Commonality Program, visit https://acc.dau.mil/commonality.
Editor’s Note: Articles in Media Spotlight are excerpts from publications or broadcasts that show the industry what the public is reading or hearing about fasteners and fastener companies.
Related Stories:
There are no comments at the moment, do you want to add one?
Write a comment