Boeing’s ‘Bolt Box’ Helps Ensure Safety
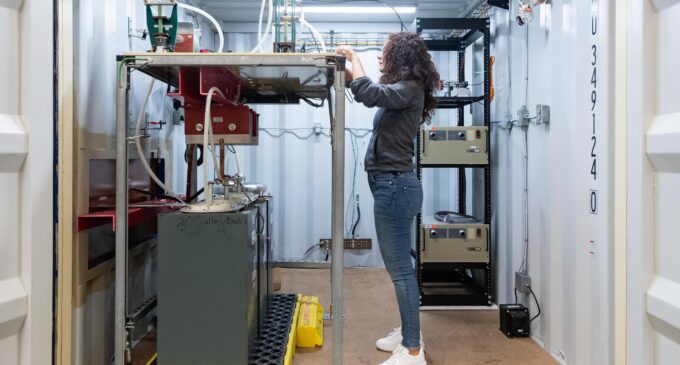
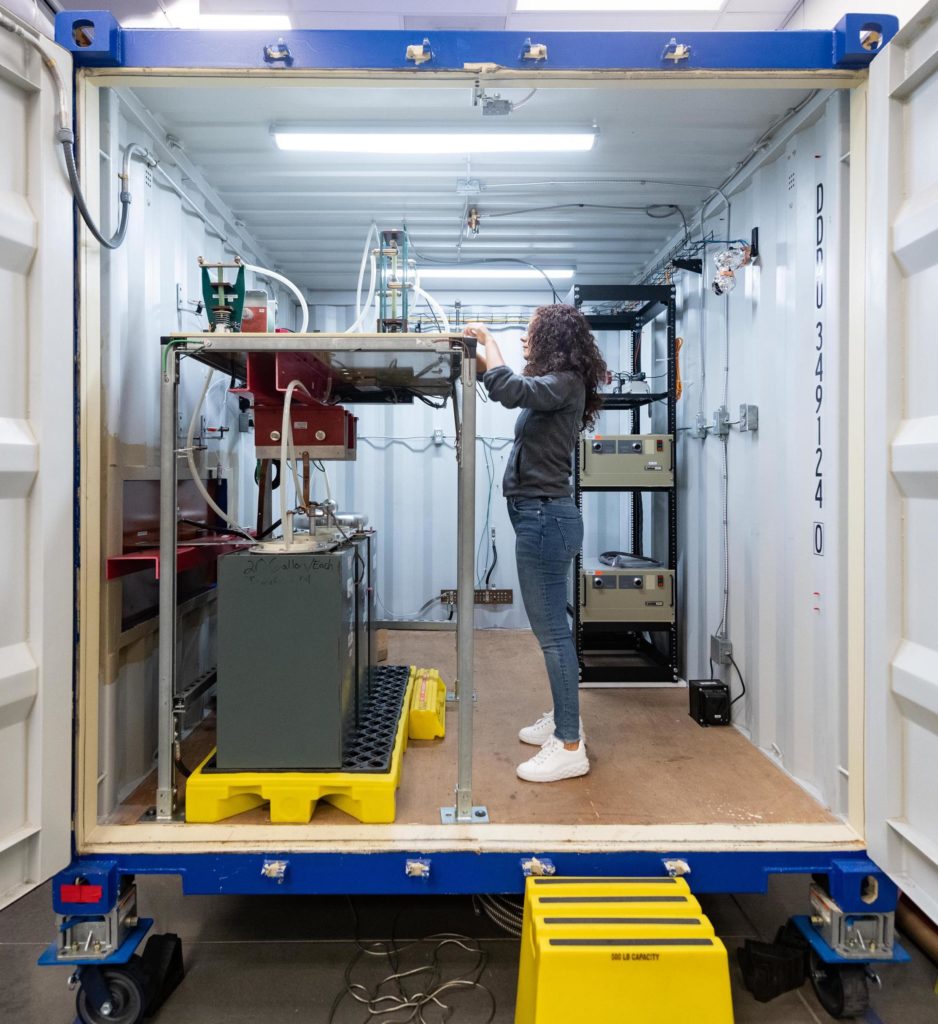
Boeing electromagnetic effects engineer Louisa Michael preparing a test in the ‘bolt box.’
What do you get when you drive lightning-level electrical current into aerospace fasteners?
For the largest aerospace manufacturer in the world, it’s data.
Just north of Charleston, SC, in one of Boeing’s lightning labs, the Electromagnetic Effects (EME) team drives high levels of electrical current through aerospace components to mimic the effects lightning strikes can have on airplanes and study how the parts respond.
“When capacitors discharge the current, the resulting strike emits a booming pop, but without the blue plasma arc typical of the bolts seen flashing across the night sky,” according to Boeing writer Maksim Goldenshteyn.
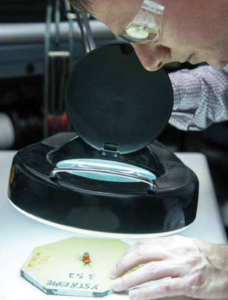
Boeing electromagnetic effects engineer Ben Westin examines a threaded insert after introducing high levels of electrical current.
While natural lightning strikes carry millions of volts and billions of joules of energy, Boeing’s lab strikes are scaled for safety so the results can be extrapolated mathematically to predict what might happen in the real world.
Airplanes are designed to withstand lightning strikes, with ground inspections used to identify any potential damage and determine if repairs are needed.
The EME crew’s research informs how parts are designed, the recommended allowable damage limits, and maintenance and repair practices.
The experiments take place in an enclosed shield room, with engineers observing from a separate wing of the facility. A thermal camera measures how lightning heats up each part. A high-speed camera takes footage of flying particles. And an open-shutter camera captures all light emitted – from the moment the current strikes the material and sparks to outgassing.
Boeing has an ongoing interest in fastener design and testing. Fasteners played a prominent role in the nearly three-year delay of the Dreamliner as supply disruptions and improper installation plagued its test aircraft fleet.
Boeing had an issue with overtorqued fasteners in some of the first 787s. The aircraft manufacturer discovered that hairline cracks in wings “stemmed from fasteners used to connect aluminum shear ties on the wing ribs to the carbon fibre composite wing panel,” according to the Wall Street Journal.
“The fasteners were over-tightened without the use of manufacturing fillers, compressing a gap in the structure and in some cases caused hairline cracks of less than an inch: if left unchecked it can cause unintended stress on the jet’s structure and lead to further damage.”
Likewise, an “unusual production mishap” on the 787 assembly line in Everett, WA, revealed a continued problem with incomplete fuselage sections from Boeing’s South Carolina facility, according to the Seattle Times.
“During 787 assembly, before the point where all the fuselage sections and wings are joined to make the complete airframe, the fuselage sections are held in place by cradles,” wrote Dominic Gates of the Times. “After the join is made, the cradles are lowered and removed.”
However, when mechanics in Everett removed the cradles, “nearly 100 improperly installed fasteners clattered to the factory floor.”
“A subsequent inspection found the South Carolina team in Everett had installed hundreds of temporary fasteners near the join between the two aft fuselage sections without the collars needed to hold them in place,” according to the Times.
There are no comments at the moment, do you want to add one?
Write a comment