The Future of Mechanical Fasteners
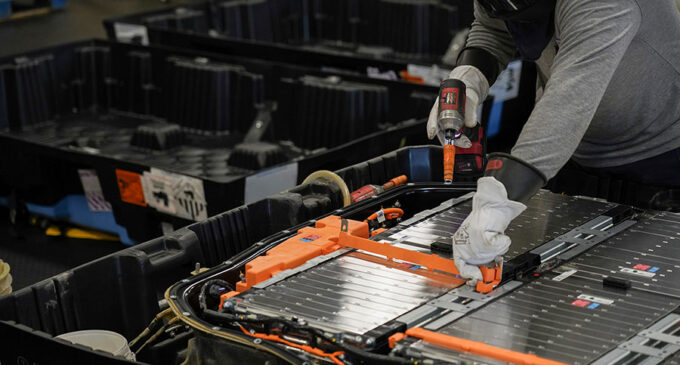
In the EV market, the mechanical fastener industry plays a vital role by providing products that are lighter, stronger and simpler to manufacture through faster automated and manual installation, according to Assembly Magazine.
“Unlike other assembly processes, such as adhesive bonding, riveting or welding, fastening is ideal for electric vehicles, because it enables engineers to join a variety of lightweight, dissimilar materials,” Assembly reports. “Mechanical fasteners also address recycling and sustainability issues, since they allow battery packs, traction motors, thermal management systems and other components to be easily disassembled.”
Automakers need fastener suppliers to innovate in materials science and engineering for incremental weight savings while bearing greater loads and stresses. And EV fasteners must protect components against the elements.
“The EV market continues to provide great opportunities for us to introduce innovative fastening technologies,” says Gene Simpson, president of Semblex Corp., told Assembly.
Optimas Solutions recently worked with one manufacturer to reduce a fastener’s weight by 43%. The entire piece was “reimagined from the material to the type of drive head while maintaining the strength requirements.”
Profil North America, a division of PennEngineering Co., worked with a European OEM for months to develop a fastener with a metal-to-metal watertight seal that joined the battery tray to body panels formed with press-hardened steel — without sealants or adhesives, Assembly reports.
The solution was to stamp a hexagonal opening instead of the usual circular opening, to give the fastener more grip, and redesign the fastener to match up with the new site.
Read the full Assembly article here.
There are no comments at the moment, do you want to add one?
Write a comment